工厂行车如何释放空间潜能?3大创新场景深度解析
发布时间:
2025-07-21
在现代工厂的物流体系中,行车如同无形的“钢铁手臂”,其运作效率直接决定着全厂的生产效能。随着制造业向高质量发展迈进,行车技术创新正围绕立体空间利用、复杂工况适应、智能精准控制三大方向突破,为工厂物流注入全新动能。
在现代工厂的物流体系中,行车如同无形的“钢铁手臂”,其运作效率直接决定着全厂的生产效能。随着制造业向高质量发展迈进,行车技术创新正围绕立体空间利用、复杂工况适应、智能精准控制三大方向突破,为工厂物流注入全新动能。
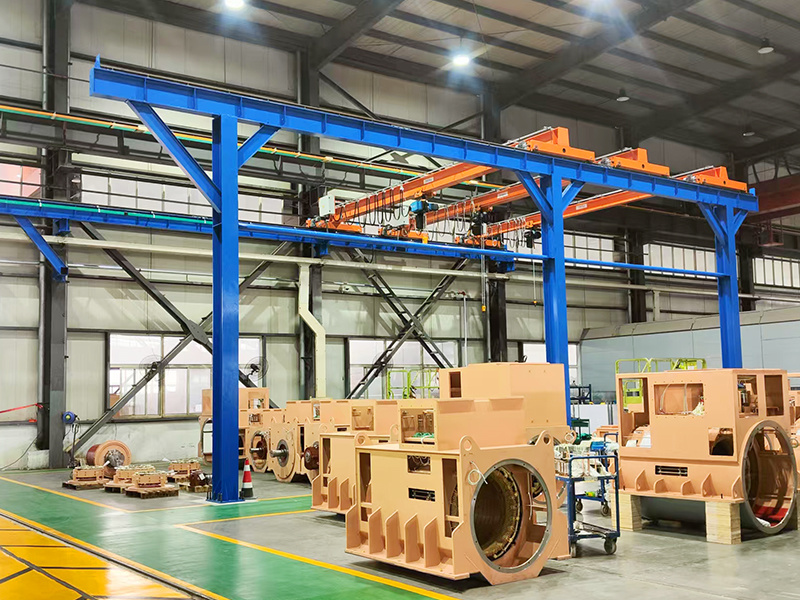
空间重构:从平面搬运到立体协同
在厂房高度受限的作业环境中,新型行车系统通过结构创新实现空间极致利用。行业案例显示,多向平衡技术能以不足2.7米的轴距实现7吨级载荷搬运,配合全向驱动功能,在传统设备难以周转的狭窄区域完成长物料转运。更突破性的应用体现在高铁桥梁制造领域——双机同步搬运系统通过毫米级协同控制,使两台大型行车实现整体储槽的直接移运,相比传统分段吊装减少30%中转环节。新型装卸装置则突破空间限制,仅需单侧通道即可完成整卡车装卸,有效解决双通道不可用的工厂痛点。
工况征服:从稳定运行到全场景适应
面对工厂复杂环境,行车设备通过结构创新展现强大适应性。千吨级门式起重机采用单梁优化设计,通过智能算法分析多工况应力分布,配合实时姿态监测系统,保障在滨海高湿、多风环境中的稳定运行。针对木材厂、金属场等崎岖路面工况,新一代设备融合悬挂系统优化与大直径轮胎,配合可旋转座椅设计,显著降低驾驶员长时间作业疲劳度。在风电施工现场,特殊设计的支腿结构能确保在松软地基上的稳定支撑,实现50米基坑内的精准吊装。
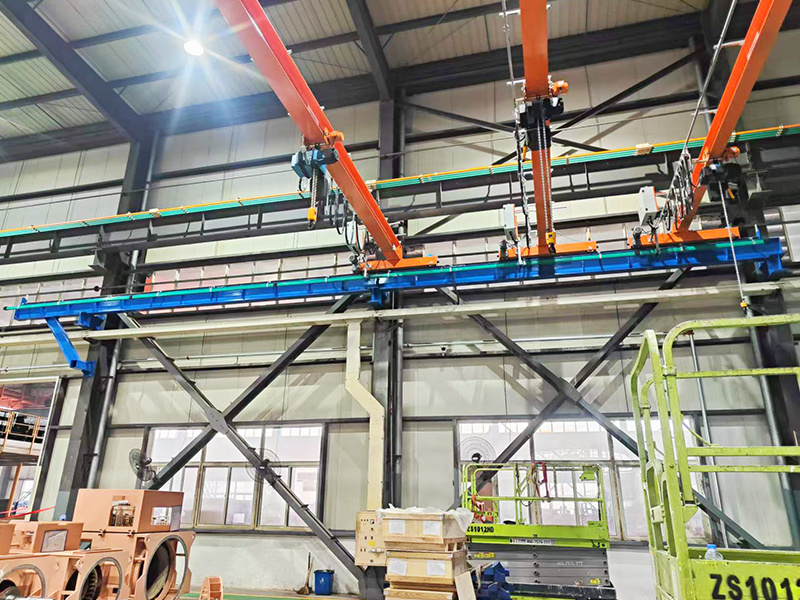
智能进化:从人工操作到自主决策
智能化正重塑行车的“神经中枢”。高铁施工现场的行车系统集成北斗+激光定位技术,将吊装误差控制在毫米级,满足重大工程建设的精度要求。更前沿的吊钩防摆技术通过实时感知负载状态,自动调整运动姿态,使吊钩最大摆动角度小于3°,典型工况效率提升显著。新一代控制系统运用多传感器融合算法,实现毫米级障碍物识别,在动态环境中自主规划最优路径。
产业实践印证:空间经济学、人机工程学与智能控制技术的融合,正在重构工厂物流体系。 据行业报告,应用智能监控系统的工厂安全隐患显著降低,设备突发故障停工时间减少明显。
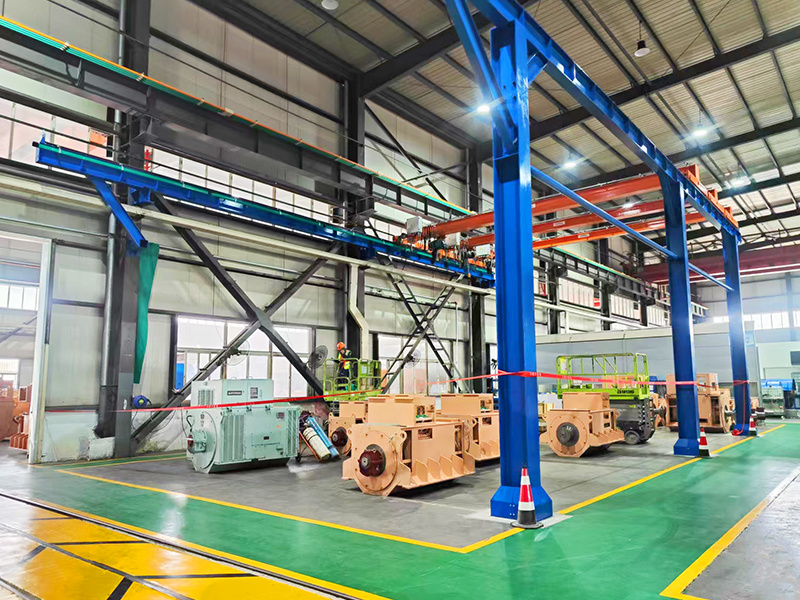
当行车学会思考、适应与协同,工厂的每一寸空间都释放出倍增效能。在政府推动的“智改数转”政策引导下,起重行业数字化转型正加速推进,这场由智能化驱动的空间革命,将持续提升中国制造的效能水平。
对于寻求轻量化、智能化升级的企业,选择适配的行车解决方案尤为关键。 科尔智能专注于轻型起重领域的专业服务商,可提供从KBK起重机到智能行车的全品类设备,覆盖设计、制造、安装到售后维保的全生命周期服务。这种“一站式”的起重运输及物料搬运解决方案,能精准匹配不同工厂的空间结构、工况需求与智能化升级路径,帮助企业快速实现物流效能跃迁。
上一条