KBK柔性起重机:模块化设计如何让车间效率飙升?
发布时间:
2025-06-23
在刚性与柔性的较量中,KBK柔性起重机凭借卓越的模块化设计,成为驱动现代车间高效运转的强大核心,让效率提升之路,清晰可见,触手可及。
想象一下: 在繁忙的汽车零部件车间,老旧起重机横亘头顶,笨重僵硬,无法适应新增工位。工人们在狭窄通道里艰难推送满载轮毂的小车,刺耳的金属摩擦声此起彼伏——直到灵动的模块化轨道蜿蜒伸展至新区域,变革瞬间激活。这正是KBK柔性起重机用模块化设计,破解空间困局、释放效率潜能的生动写照。
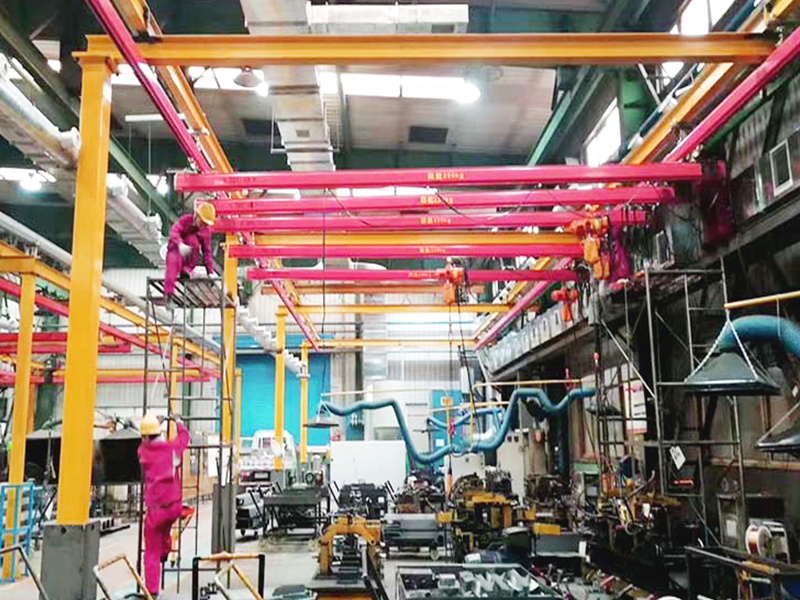
一、空间魔法:布局难题,轻松化解
改造传统起重机?往往意味着停产、拆顶、大动干戈。KBK带来的变革截然不同——仅需三天,焕然一新!当新增检测工位打乱原有动线,无需大规模拆建。只需像拼接“工业乐高”:在现有直线轨道上,轻松接入3段定制弯轨 + 1套双梁吊架,一条流畅的U型转运通道即刻成型。秘诀在于KBK的标准化接口系统:所有核心部件(轨道、主梁、行走机构)采用统一接口,兼容性强,连接无忧。
更妙的是,所有模块仅靠预紧式螺栓连接,全程无需焊接、不动厂房结构。车间照常运转,两名安装工仅用一个周末,用普通扳手便完成了华丽升级。周一开工,工人轻按遥控器,吊钩便轻盈滑过新轨道,将轮毂精准送达检测台。成果立现:空间利用率↑27%,跨工位转运时间↓40%!
二、动态升级:生产线随需而“长”
当新能源电池盒订单激增,原有设备“力不从心”,无法吊起增重30%的新壳体。传统方案?整机报废,代价高昂。KBK的模块化设计则展现出强大的适应性。解决方案简单高效:保留主体轨道,仅两天时间,换上强化型主梁与2吨级环链葫芦。巧妙之处在于:针对厂房立柱遮挡区,增设自立式支撑架,延伸出8米分支轨道,巧妙绕过结构障碍。
这种“渐进式升级”带来实实在在的成本节省:相比整机更换,投入直降35%。改造期间,产线产能依然保持70%以上,损失微乎其微。模块化的精髓正在于此:产线扩展如同插入新积木般简单——未来新增装配机械臂的接口?早已预留就绪!
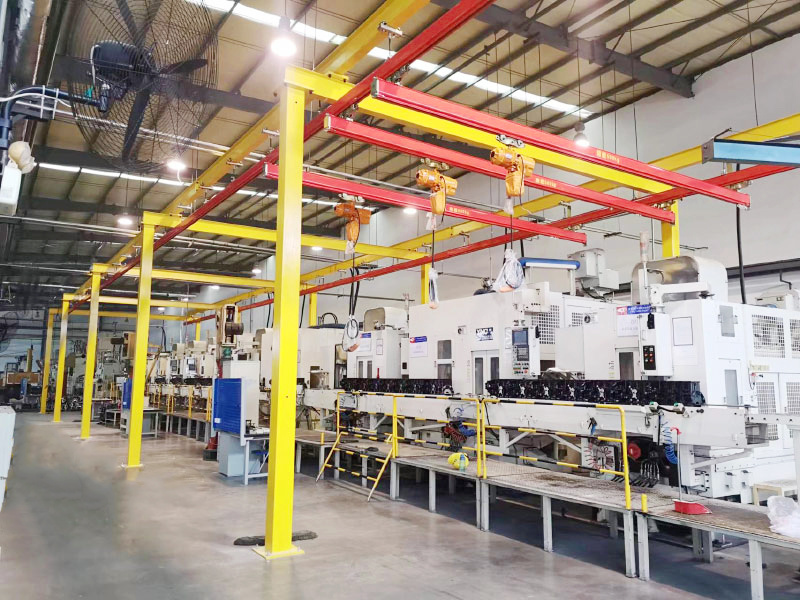
三、快修保障:故障停机,大幅缩减
一次冬季突发状况成为完美检验:一台起升电机低温罢工。若用传统设备?搭脚手架、拆横梁,停机漫长。而KBK的快拆插销设计力挽狂澜:维修工仅四步操作——断电→拔插销→滑出故障模块→推入备用单元。整个过程压缩在关键的90分钟内,便捷如同更换打印机墨盒!
背后的智慧在于:电气线路采用航空插头盲接,即插即用;机械连接依靠自对准锥形销,精准快速。这不仅极大缩短修复时间(MTTR),更让备件库存需求锐减60%——通用模块,灵活调配,库存压力大减。
夜幕中,智能KBK轨道轻盈绕过新风管道,将最后一托货物精准送入物流区。 这场景,正是柔性价值的完美诠释:
订单变化? 模块随时重组,灵活响应!
设备故障? 单元快速替换,停机最短!
工艺升级? 功能无缝拓展,投资增值!
在刚性与柔性的较量中,KBK柔性起重机凭借卓越的模块化设计,成为驱动现代车间高效运转的强大核心,让效率提升之路,清晰可见,触手可及。